Aircraft Hydraulic Failure
Aircraft Hydraulic Failure
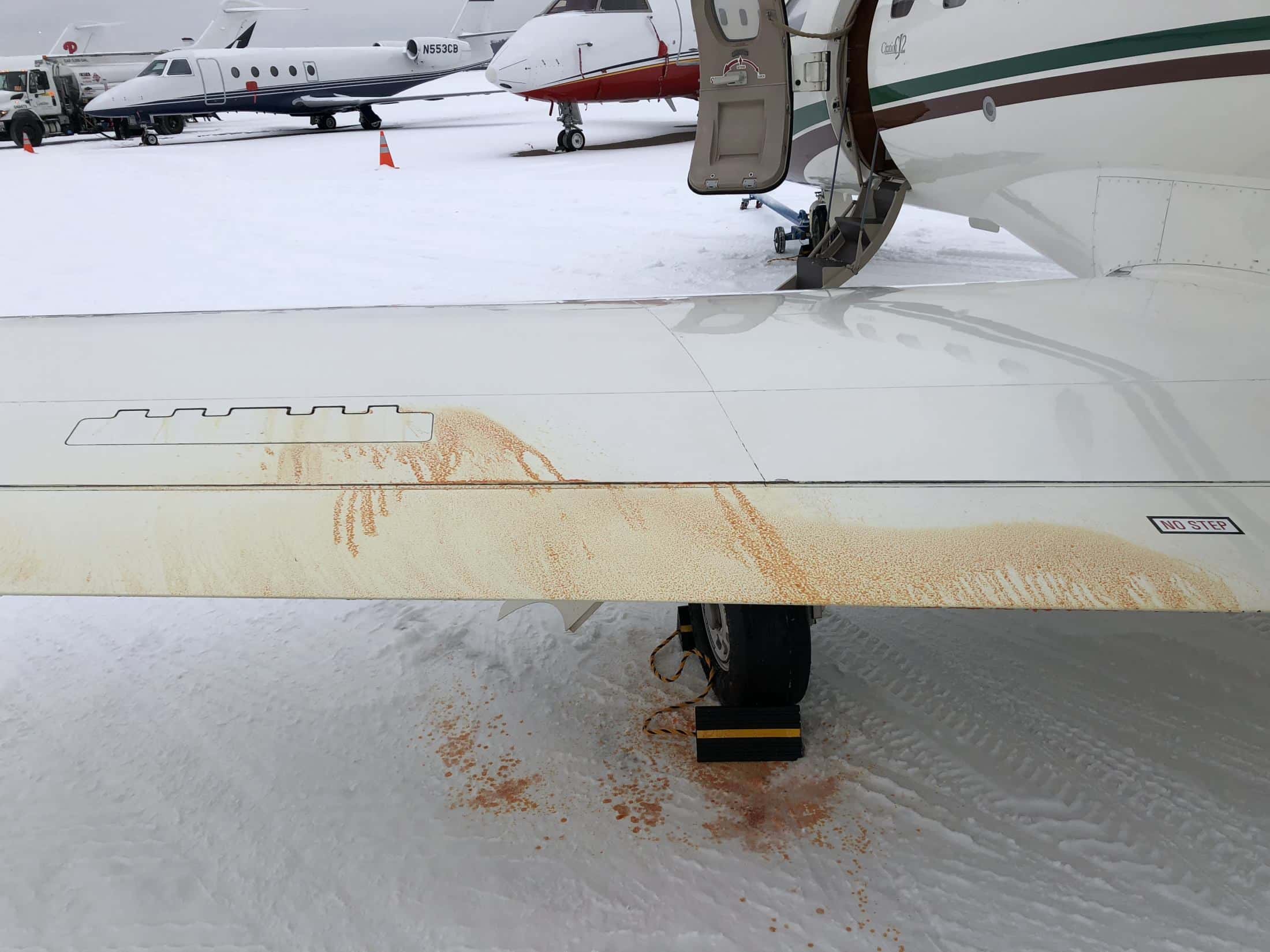
Hydraulic failure in an aircraft, involving the malfunction or loss of hydraulic systems, can lead to reduced control, increased workload for pilots, and potentially catastrophic outcomes, especially during landing. These systems are crucial for operating landing gear, brakes, flaps, and flight control surfaces.
What are hydraulic systems?
Aircraft hydraulic systems use pressurized fluid to power essential mechanical and electrical components, including flight controls, landing gear, and brakes.
What happens during a hydraulic failure?
- Loss of control: Pilots may face compromised control over the aircraft, significantly reducing its maneuverability.
- Landing gear issues: Difficulties with extending or retracting landing gear can occur.
- Braking problems: Reduced braking capability upon landing is a potential consequence.
- Other issues: Loss of autopilot, partial control over different control surfaces, and lack of control over thrust reversers are also possible.
Redundancy and Safety
Modern aircraft often have redundant hydraulic systems to mitigate the effects of a failure. If one system fails, another can take over.
Examples of Hydraulic Failure
- Atlas Air Boeing 747-400F: In June 2024, an Atlas Air Boeing 747-400F experienced a serious hydraulic failure shortly after takeoff from Hong Kong International Airport, prompting a return and emergency landing.
- Air India Express flight: In October 2024, an Air India Express flight experienced a mid-air hydraulic failure, resulting in an emergency landing.
Real-life consequences
Hydraulic failures can lead to significant delays, as seen in the Atlas Air incident, and can also have serious safety implications.
Importance of Redundancy
The importance of redundant systems in modern aircraft is highlighted by incidents like the Atlas Air and Air India Express flights.