X-Ray Inspection
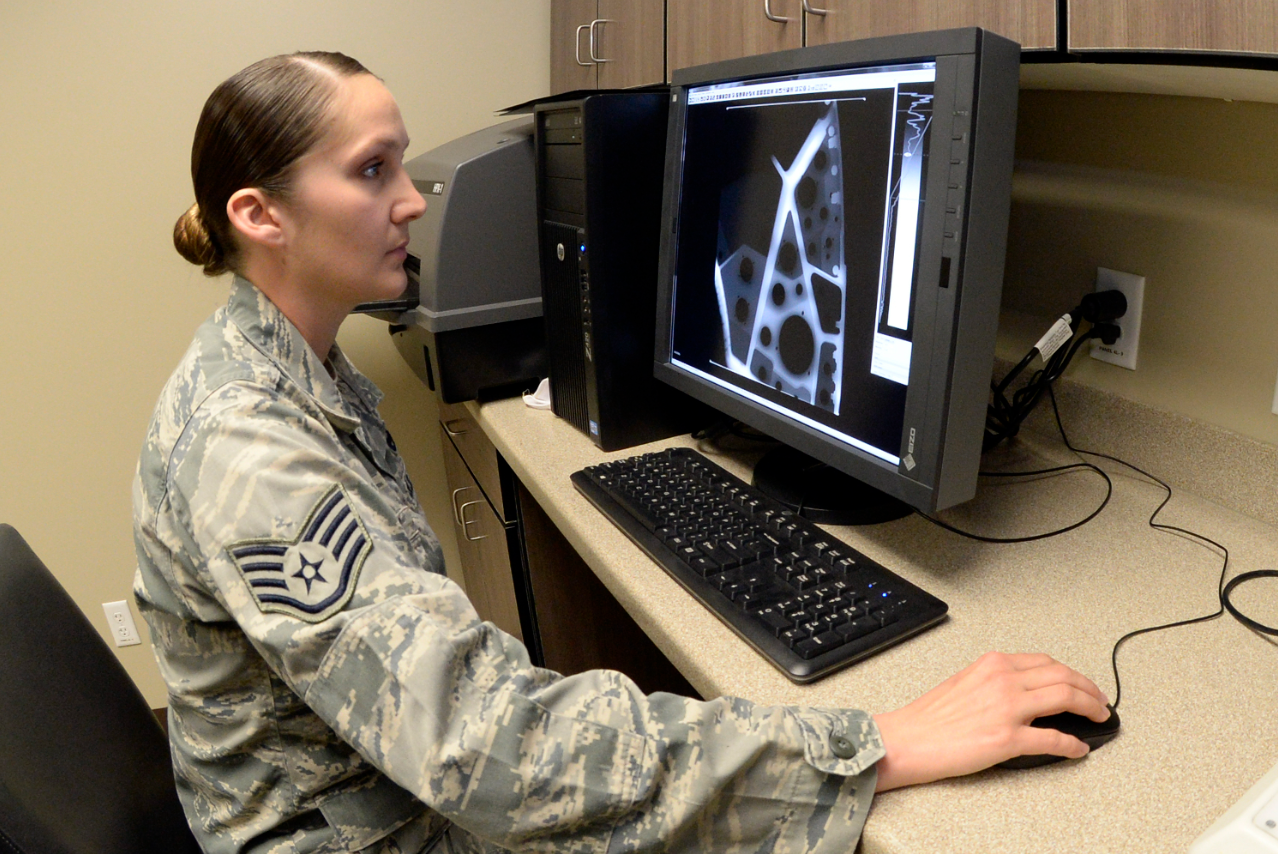
X-ray inspection in aviation has a rich history, starting with the discovery of X-rays by Wilhelm Roentgen in 1895. Initially used for medical imaging, X-rays soon found their way into industrial applications, including aircraft manufacturing and maintenance, to detect internal defects like cracks and flaws. This technology became particularly vital during World War II, when reliable aircraft inspection was crucial. Post-war, commercial aviation's growth spurred the development of more sophisticated X-ray inspection methods, including digital radiography and computed tomography.
Early Development (Pre-1940s)
- 1895: Wilhelm Roentgen discovers X-rays.
- Early 20th Century: X-rays are first used for inspecting aircraft components.
- 1930s: George E. Newton founds Aircraft X-Ray Laboratories (AXL) with the goal of inspecting castings before machining to catch defects early.
World War II and Beyond (1940s–1960s)
- World War II: X-ray inspection becomes crucial for ensuring the reliability of aircraft during wartime.
- Post-War: Commercial aviation expands, leading to a need for more rigorous inspection methods.
- 1960s: X-ray baggage scanners are introduced in airports due to rising concerns about terrorism.
Technological Advancements (1970s–Present)
- 1970s: Low-dose X-ray scanners are developed for baggage screening at airports.
- 1980s–Present: Digital radiography and computed tomography (CT) are developed, providing faster and more detailed inspections.
- 2000s–Present: X-ray inspection continues to evolve with advancements in technology, including the use of X-ray fluorescence (XRF) for more precise analysis of materials.
Applications in Aviation
Manufacturing: Inspecting raw materials, welds, and castings for defects before further processing.
Maintenance and Repair: Detecting corrosion, cracks, and other damage in aircraft components during routine inspections.
Research and Development: Studying materials and structures to improve aircraft design and performance.
Airport Security: Screening baggage and passengers for weapons and prohibited items.